Manufacturing secrets
We've been designing and manufacturing quality children's shoes since 1870. A know-how handed down from generation to generation. From the first sketches to the finishing touches, one model requires over 200 different stages of production. Sometimes unsuspected, always demanding. We wanted to share a little of our passion for this exceptional craft.
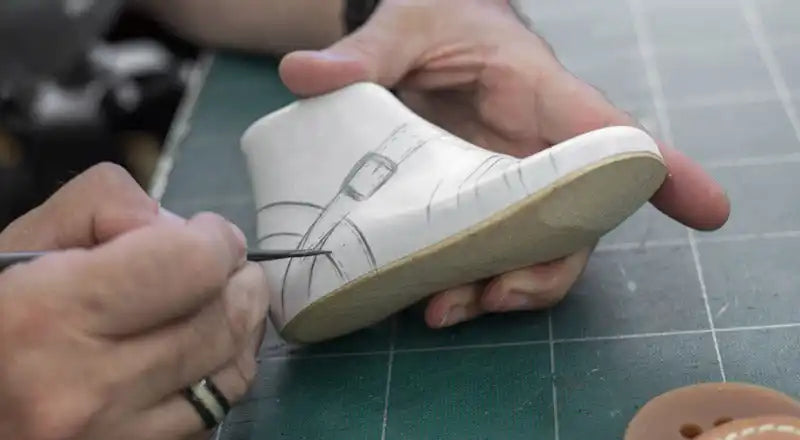
Form drawing
It all starts with the expertise of the shape. The first idea of the shoe must be materialized in the form of a volume. This is a vital and extremely precise stage. The width of the shoe, the volume of the instep and the degree of forward lift are all characteristics to be taken into account: to the millimeter! Next, a plastic shell is molded onto the last to enable the pattern maker to draw the upper.
From the sketch provided by the styling department, the pattern maker will reproduce the upper on the last using a fine graphite pencil. Years of experience are needed to acquire the precision required for last drawing. The shoe will be identical in every detail to the result obtained.

Patronage
An adhesive fabric is applied to the form. This allows all the elements of the stem to be transposed by transparency. Carefully peeled off, the canvas is then applied to cardboard. After precise cutting, the shoe pattern is created.
CUTTING
The elements obtained enable the cutter to cut each piece of leather that makes up the shoe upper. This includes the inner linings. Once the pattern has been created for a given size, called the base, the dimensions of the pieces needed to make the adjacent sizes are obtained by graduation. Several closely spaced bases are essential for the realization of a range of sizes, as foot morphology evolves enormously in the early years. Each of these bases will be drawn to shape and patterned. Once the first sample has been assembled, several fittings are carried out to check the model's shape and fit. This is called "fine-tuning". The pattern maker makes any necessary modifications to the basic pattern.
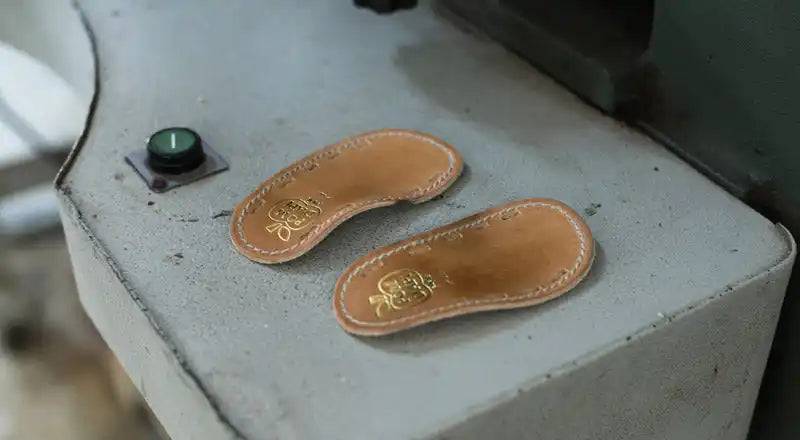
To stitching and assembly
To sum up the various stages: the idea is materialized in a form, on which the pattern maker draws the stem. From this drawing, a pattern is created, from which all the parts of the stem are cut. At the same time, the "première de propreté" is also prepared. By adding the other elements that may make up the model, such as the heel counter and the toe cap (rigid pieces that are placed respectively on the heel and on the front of the shoe between the lining and the leather) or the fastening elements (zip, buckle, eyelets...), the model is ready for stitching and assembly.
All the separate elements that make up the shoe are prepared, and now it's time to assemble them. The upper is the first part to be built. A final preparation step is then necessary for the leather parts that are to accommodate a particular strap or lacing.
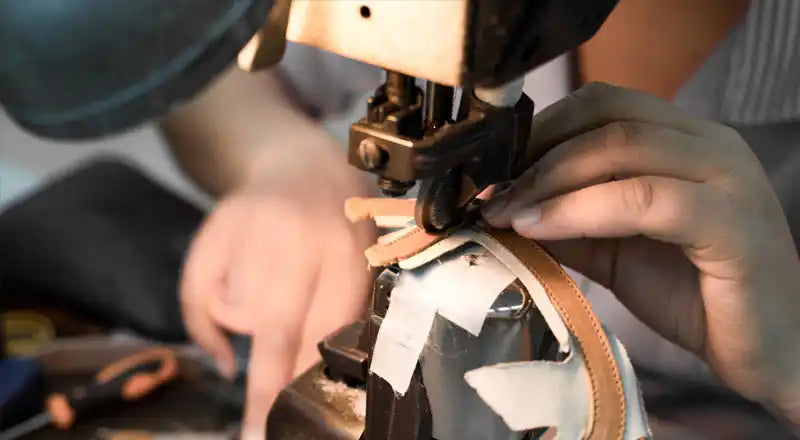
The sting
The pieces of leather that make up the upper, both outer and lining, are assembled in the stitching workshop. Stitching requires great dexterity and precision in every gesture to guarantee a quality result. The stem is then positioned on a plastic form, ready for assembly.
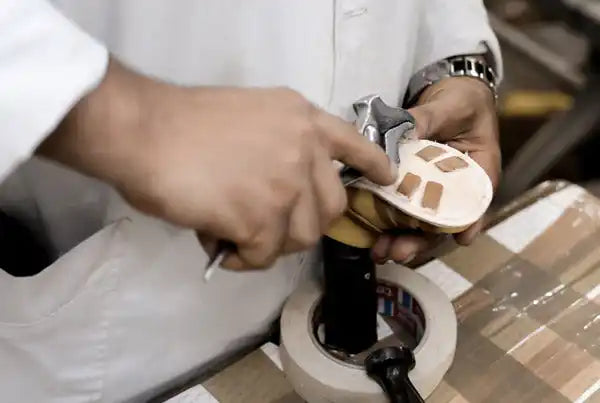
Assembly
Assembly consists of joining the stem and the first assembly. There are different types of assembly, each with its own particular characteristics depending on how the stem and first are assembled.
In brackets
From stitching to assembly, there are a multitude of operations that we haven't mentioned here. Yet each of them has a necessary place in the manufacturing process. For example, once the upper and lining are assembled, all the edges are hand-dyed with a brush, using a mixture of natural dyes similar to the color of the leather. This meticulous attention to detail is an integral part of product quality.
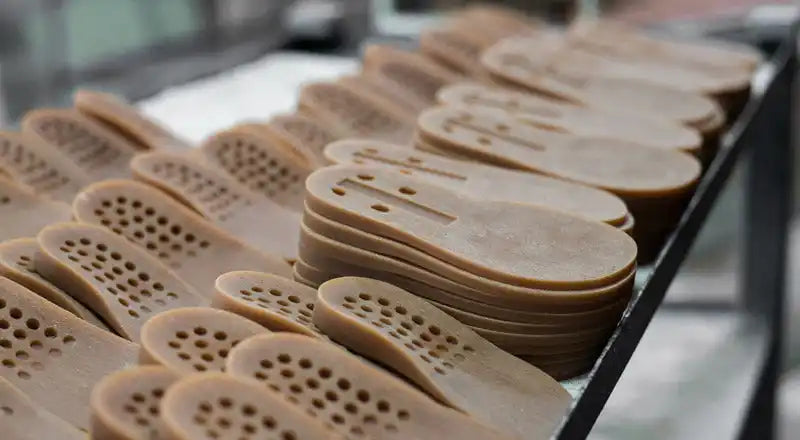
Construction
The final stage in the manufacturing process consists of assembling the outsole, or outrigger, to the newly-formed stem-insole assembly. In traditional assembly, the outsole is glued to the upper. This is known as welded construction. This requires a great deal of rigor and preparation upstream to ensure a perfect sole-stem bond. Carding, for example, consists in lightly sanding the underside of the insole before it is put in the oven, to help the glue adhere better.
The first assembly is held to the form by adhesive strips. The rod is then fitted to the form, covering the first assembly. The whole assembly is then hot-glued together. Once cooled, the assembly is either glassed or carded, as required. Leather or cork filling completes the process, making the assembly homogeneous. Next, the sole and the insole are glued together, then left to rest to release the solvents. Finally, these two elements are assembled, the glue reactivated and pressed together.
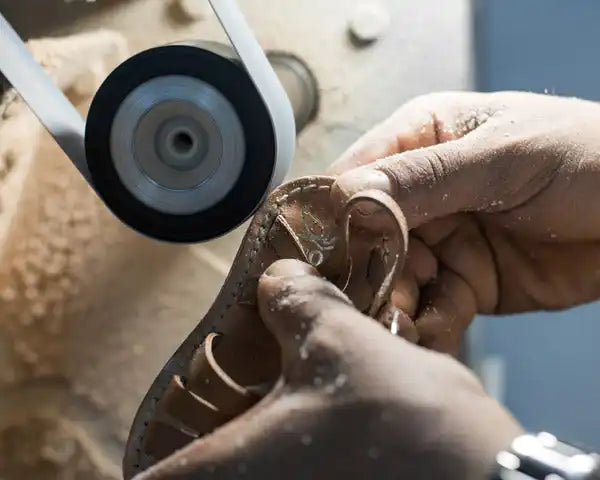
Finishing
The pair is then cleaned and pampered by hand, depending on the final appearance the leather is to have. All these different treatment operations are called finishing.
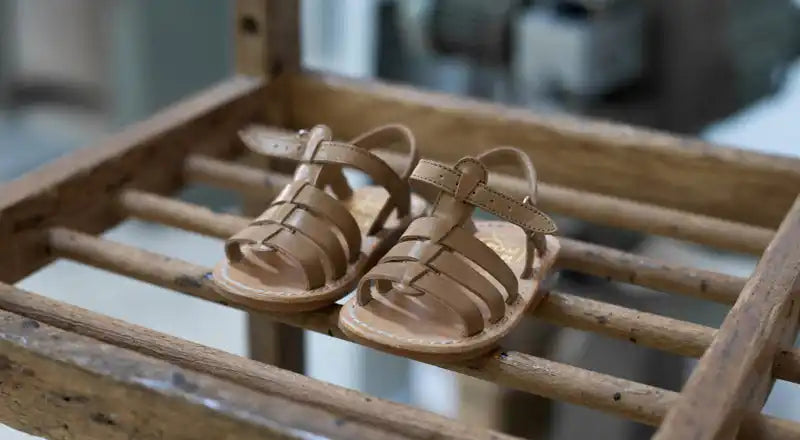
Canning
Once the finishing touches have been made, the pair of shoes is meticulously checked for any manufacturing defects. They are then carefully wrapped in tissue paper and boxed. This seals the more than 200 steps involved in its manufacture.